
XL810
XL810 - real-time data for production and performance management
XL is the simplest, fastest, and most powerful way to monitor and improve manufacturing.
XL810 is a bolt-on smart device that includes onboard I/O to monitor your process.
It provides you with a scoreboard for a true visual factory, factory wide real time data and reports for managers to drive continuous improvement.
IoT that scales from machine to enterprise.
Monitor any machine. Anywhere.
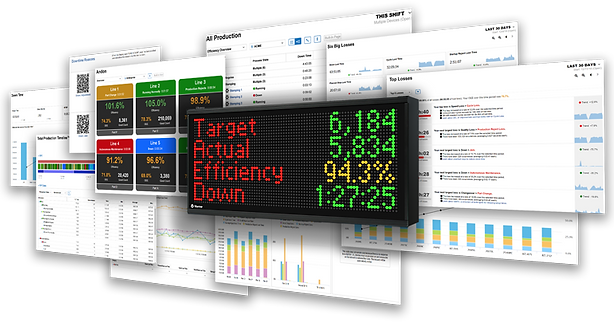
Features
-
Accurate OEE and downtime data
-
Real-time results on factory display motivates the team
-
Real-time & historical results on web interface
-
Instant customisable web reports.
-
Teams & Labour
-
Customisable web dashboards
-
Email / Text Alerting
-
Export to Excel
-
Self deployed in hours, not weeks
-
Super easy to install and use
-
No software to install
-
Tried and tested for over 15 years
-
Bolt-on. This won’t shut your process down
-
A complete solution in a box
-
No ongoing expensive software licence fees
-
Unlimited users
-
90 Day trial
-
My manually collected data is not accurate enough.LineView features fully automated data and down reason tracking without operator intervention.
-
I need the next level of detail for machine stops.LineView features automated trending of PLC fault codes on each machine
-
I can’t see all my live and historical factory information in a single place.LineView features an overview of the entire plant and lines on one screen, with drill-downs to machine level.
-
Our current system takes too long to get usable info out so it isn’t used properly.LineView excels at condensing the critical data that you need to see how your line has performed, what the true losses are, so you can quickly make decisions on what improvement actions can be taken. Live screens are presented in a useable, easy-to-read formats. Predefined reports are standard.
-
Our current system isn't real-time.Real-time and accurate data visible across your business via a web interface.
-
Current system is more focused towards the engineering team - not the manufacturing team.LineView does both. Key data for on-the-floor team, together with in-depth machine fault detail and further comment entry for engineering. Everyone using the same system.
-
Our current system doesn’t have overall line performance.With true causal downtime and real-time 6 loss analysis at the constraint machine, LineView identifies which machine is having the greatest impact on overall line productivity.
-
We have an existing system on some lines but this can’t be used on lines from other machine suppliers.LineView can be used on any machine or line and is not OEM dependant.
-
We need more detail than the PLC fault code.In addition to the automated fault codes, LineView enables you to add further comments, record actions, and select predefined categories for events.
-
We don’t have all the data we need to drive continuous improvement.LineView tracks OEE, Efficiency, speed, downtime, planned stops, rejects, MTBF and more.
-
The cost is prohibitive.LineView is scalable from two machines to many on a line, so you only pay for what you need and can grow it at any time.
-
We're not using the information our current system provides very well.LineView offers built-in management routines, action tracking, assigning of targets, and responsibilities.
Empower and Motivate Operators
Are you doing a lean thinking, lean manufacturing, productivity improvement, six sigma programme?
Having a highly visual workplace is a critical part of a lean or continuous improvement journey, and is key to engaging and motivating your team.
The team and each individual team member must be able to see and understand, at a glance...
-
how they should be going, what is the target?
-
how they are actually going relative to the target? In front or behind?
The scoreboard display gives this real-time information to the operators, helping them to 'Self Measure'.
This in turn can change their behaviour leading to 'Self Improvement', quickly driving the 1st stage of improvement in productivity.
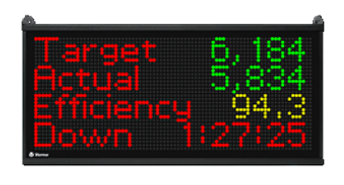
Easy for Operators
If using a system is too hard, it won't get done.
XL makes it easy for the operators to gather accurate reasons for downtime.
No more manual recording. No more fighting with screen savers and passwords.
Simply scan a barcode.
You can also enter additional comments to add more info, context, actions etc to an event
Option available to enter data from a tablet or HMI

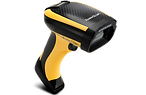

Easy for Team Leaders and Management
If trying to find data and getting reports is too hard, it wont get done.
XL makes it easy for anyone to quickly access data and reports to be used in the continuous improvement process.
Problems at a glance
What problems are resulting in the target not being met?
Summary and deep dive downtime and top losses reports
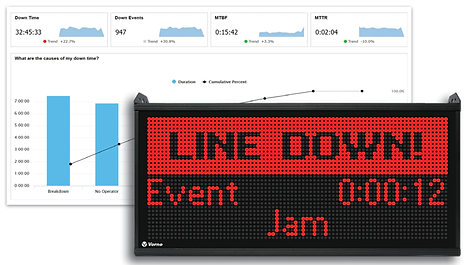
Instant trend charts
What impact are the problem solving actions having on OEE?
Historical trend charts on 100+ KPI's
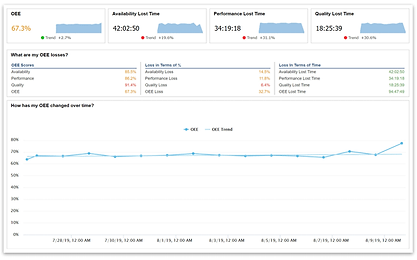
Instant Visual Factory
Which line needs more support today?
Live Factory Dashboard in your factory, offices, meeting rooms.
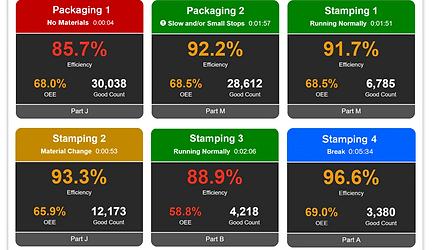
Instant Reports
How long should you spend on preparing shift, daily, weekly and monthly reports?
The information you need at your fingertips, using one of the built in dashboards or reports, or, create your own custom reports for anyone in the business.

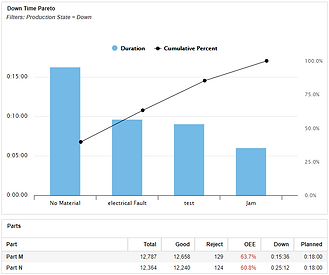
Easy for Super Users
No script or coding.
Just simply point and click to add new down reasons, add a new part, change a target time and more.
Help tool tips, and videos are built in to assist you.
Point and click Admin changes

Live reporting
Built-in and customisable web based reports enable you to get your information quickly to make continuous improvement decisions. Click this link to see more
XL bolt-ons
XL is a fully self contained system with everything you need built right in.
A suite of Bolt-on solutions allows you to integrate and automate with outside systems.